Jobs
EMAG grinds down a job shop’s price per part – Engineering.com
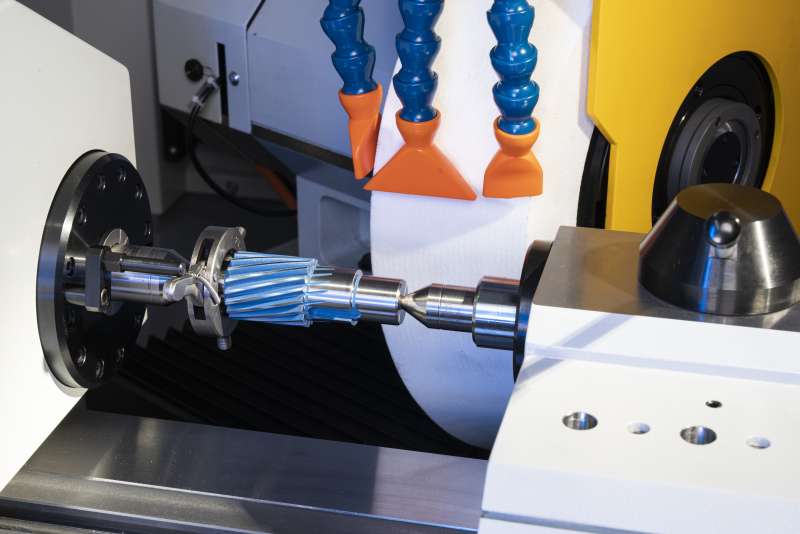
A new, compact grinding machine, being unveiled at IMTS 2024, makes big promises.
EMAG has sponsored this post.
For job shop owners, few values keep them up at night more than the cost per part. It doesn’t matter if they focus on high-volume, small batches or mid-sized orders; if they need to make a part, the economics behind that part will be of primary concern.
With that in mind, EMAG will unveil its latest WPG7 grinding machine at this year’s IMTS. Engineering.com sat down with the company’s head of Grinding Business, Bernd Dürr, and its technical sales manager of Universal Grinding Machines, Andreas Hessling. The topics of discussion were the benefits of this new equipment and how it will impact owners and production managers of small, medium and high-volume job shops producing grinded parts such as small shafts and pinions.
Affordable, versatile, compact and easy to install
Dürr notes that the WPG7 is very versatile. It can grind pinions, shafts and other parts up to a maximum weight of 30 kilograms (66.14 lbs). The parts can be as long as 250 mm (9.84 in) with a center height of 100 mm (3.94 in) and swivel diameter of 200 mm (7.87 in). It can also achieve accuracy at the order of microns. Additionally, due to its high-speed grinding, it can also process parts in seconds.
Hessling explains that a traditional grinding machine that would process parts at those geometries, accuracies and speeds can take up two to three times more floor space than the WPG7.
“[A] positive of the machine is its small footprint,” agrees Dürr. “This is, more or less, a very small machine.”
The size of the machine was kept to a minimum by integrating much of the grinding process into a small hood. Positioning, measurements, grinding, dressing, lubrication and coolant are all done in the same housing. Another way to keep the machine’s size small was by eliminating the ability to swivel the positioning of the grinding wheel. As such, customers can choose two versions of the WPG7: one that can perform straight plunge cuts, at zero degrees, and another that has an angled plunge cut at 30 degrees. Other machines that can swivel to make different grinding cuts need to be much larger to enable this movement.
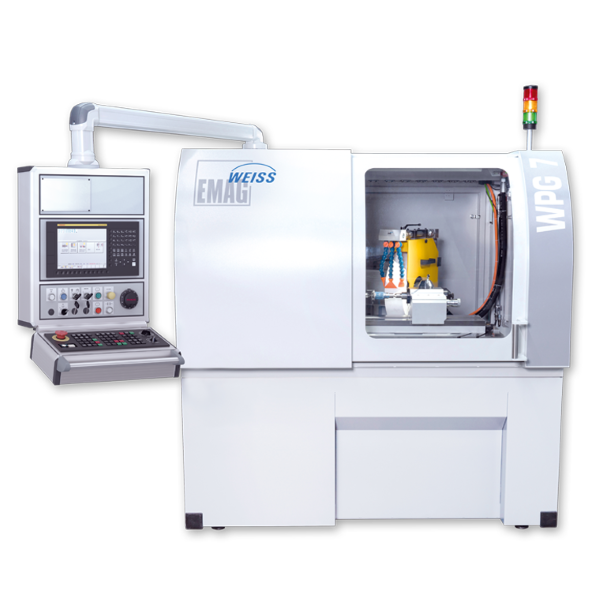
Though it doesn’t have a swiveling wheel, the WPG7 is flexible in other ways. For instance, it is compatible with cubic boron nitride (CBN) and corundum grinding wheels that are 500 millimeters (19.7 in) in diameter, with an 80 mm (0.31 in) grinding width. “This is a good advantage,” said Hessling, “that we can use both technologies on this machine.” He then suggested that this isn’t something that is standard in the industry. The ability to “mix it up” depending on which wheel works best for a given application is a bonus.
From an installation standpoint, the WPG7 is certainly in a class of its own. When other manufacturing equipment could take weeks or months to install, EMAG’s grinder takes only a few hours.
“One big advantage is that the unit only needs a forklift to pick up the new machine from the lorry,” explains Dürr. “You then set it in place, connect the power and air … then you prepare the coolant tank, and then you can immediately start this machine.”
Automated for medium and large batch job shops
The WPG7 can be run manually to optimize job shops running small batches, or it can be fully automated to produce more than 250,000 parts a year. The automation involves installing a gantry to take parts from standard and customized conveyors, robots or pickers. The gantry then places the parts into the working space before returning them to the larger manufacturing workflow after the grinding is completed. This is all done in a matter of seconds.
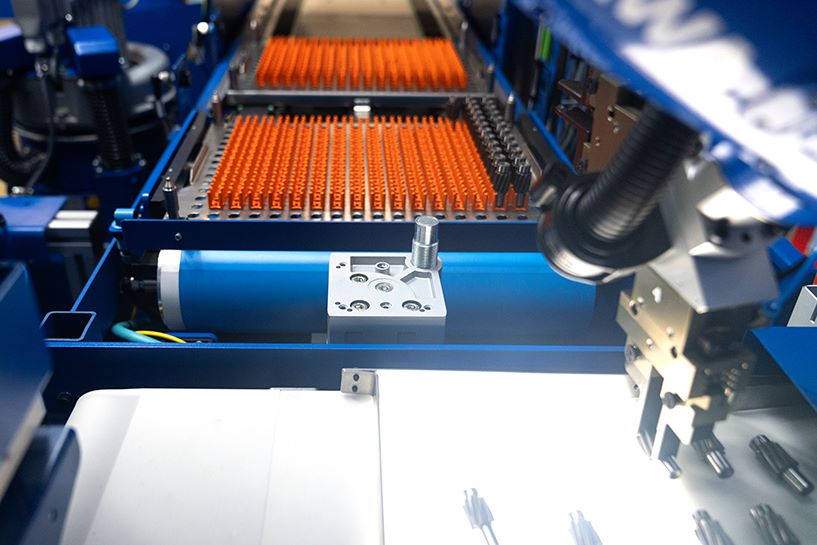
Dürr adds that the ability to automate the machine is a big advantage because it not only reduces cycle times, but also enables the machine to run without an operator. He notes that currently, finding a good operator is hard. So, by automating the machine, fewer operators are needed to get the same amount of work done.
While running in its automated mode, the WPG7 controls the path of the grinding machine, the balancing of the wheel and measures every part to ensure accuracy and to maintain safety. This is important for Hessling as it can make a job shop very effective, productive and in-demand. “If we like to keep production in our countries then we have to have automated, faster systems.” He says equipment must have “compact designs as well, because floor space costs a lot of money. So, you can have smaller job shops and bring out the same productivity.”
Easy to use for small batch job shops
Fully automating the WPG7 may not make sense for smaller batch job shops. However, the equipment can still optimize the productivity of these companies.
In this case, it might be faster for an operator to input the part, set up the machine’s path and repeat as needed. To improve operator productivity, the WPG7 has a streamlined workflow and user interface.
For example, traditional operators might have to worry about programming a grinder’s path and cycles using complex computer numerical control (CNC) codes (like G-code or FANUC). EMAG, however, addresses this by pre-programing various grinding cycles into the WPG7 that are compatible with FANUC codes.
Hessling explains, “you select the cycle, and then another page opens, and you have only to put in the size of the workpiece from the drawing, measure the length of the diameter, input diameter tolerances, the size of the grinding wheel, the width, the technology parameters (feed rate, stock, cutting speed, etc.) — everything the operator already knows for sure. And then you select ‘Run.’ If you fill in all these numbers and information, the CNC program is completely generated. This is another big point to save time and productivity.”
In other words, with a few simple inputs from an operator, the WPG7 generates its own control code. And to improve productivity, that code can be saved and reused if a particular part is ever re-ordered. In that case, all the operators would need to do is input the parts, find the correct code, and hit ‘Run.” The control system is also able to work with both metric and the imperial measurements.
Simplifying job shop workflows
Another technology that makes the WPG7 easy to operate and automate is its automatic balancing mount for the grinding wheel. As the machine continues to run, “the wheel is getting smaller and smaller and water, maybe, goes a little bit inside the wheel,” says Hessling, “When this occurs there is some unbalancing.” To address this, he says, “the balancing head is always adjusting the wheel, so you always have a good, balanced wheel. This is very important for good product quality and surfaces. It should be very accurate.”
The WPG7 also includes an acoustic gap crash sensor. As the wheel moves along its tool path, it will produce noise that can be measured. The machine software will expect to hear a lot of noise when grinding and little noise when the wheel is spinning in the air.
Therefore, based on the tool path and the part positioning, the software can listen to the noise being produced to optimize the path, reduce the gap between the part and the wheel or stop the machine if it detects a noise at an unexpected moment — indicating a crash.
Hessling explains that based on the data from this sensor, an automated feeding system can also be sped up to save time between grinding parts. Cutting the time between parts by a few seconds might not sound like much. But when a job shop processes 150,000 parts a year, that time slowly adds up to days.
If you need grinding equipment, you should see it at IMTS 2024
At IMTS 2024, EMAG can show industry leaders firsthand that the benefits of the WPG7 go beyond its compact size.
“The most important thing about this new system from EMAG is the cost per part,” summarized Dürr. “This means very low loading time, very low operating time, very good sizes, always in tolerance and the machine is able to run without an operator. Because this saves the owner of the company money, he is competitive. That is the benefit.”
To see for yourself, visit the EMAG booth at IMTS 2024 or contact their specialists for a demo.