World
Why the World Can’t Ignore the Demand for Potash
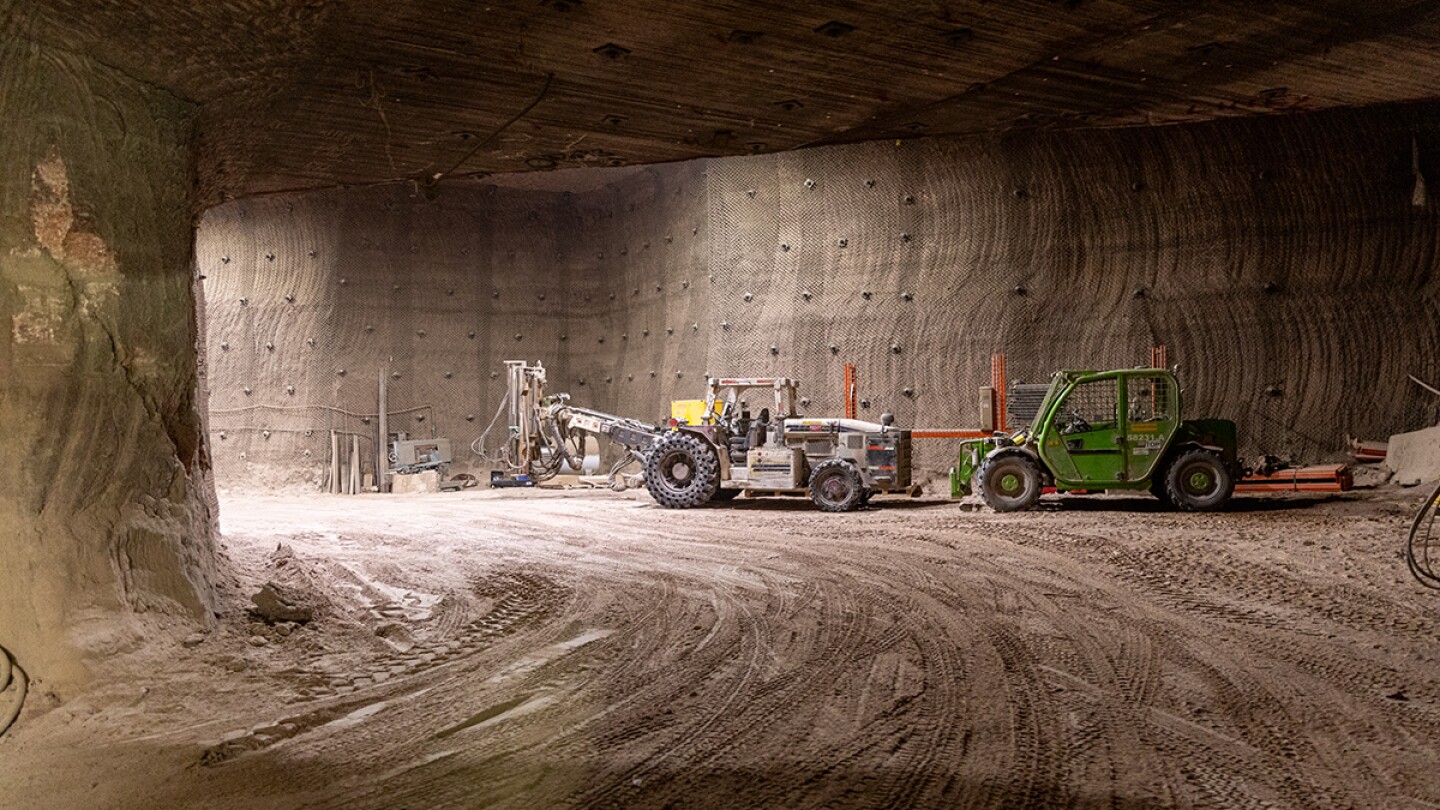
A half mile under the vast prairie soils of Saskatchewan, Canada, miners employed by Nutrien Ag Solutions work 12-hour shifts, 24/7, digging into a 350-million-year-old dry seabed to deliver a macronutrient that U.S. farmers need every year to grow high-yielding corn and soybean crops: potash.
“When you’re underground, you’ll be seeing rock that predates the dinosaurs,” Les Frehlich tells a small group of ag journalists, assembled for a tour at the company’s Allan mine, based 41 miles southeast of Saskatoon near the small town of Allan, population 625.
The group, outfitted in white coveralls, hard hats, gloves and steel-toed boots –standard wardrobe protocol for guests – is going by elevator down into the Allan mine shaft to see the company’s ore-extraction efforts first-hand.
The Allan mine harvests four different types of potash, 3.3 million tons annually, reports Frehlich, general manager, during introductory comments.
“The ore body is about 55% sodium chloride (NaCl), also known as salt, 40% potassium chloride (KCl), and then there’s roughly about 5% clay,” he says.
Global Demand
Nutrien, and therefore Canada, is the world’s largest single producer and exporter of potash, delivering it to more than 40 countries around the globe.
Canada’s 10 active mines, of which Nutrien owns six, produced an estimated 27.1 tons of potash in 2022, according to data from the Government of Canada.
The United States gets a smattering of potash from its domestic mines in New Mexico and Utah, but imports 91% of its supply from other countries, according to Statista. Of that amount, Canada supplied nearly 85% of the product U.S. farmers used in 2023.
In the U.S., about 90% of the potassium (K) fertilizer applied by farmers is muriate of potash (potassium chloride—KCL). Because it contains 60% potassium, farmers know it as 0-0-60.
Among its benefits, K supports photosynthesis, respiration, drought tolerance, crop hardiness, disease resistance and insect tolerance.
The supply of potash available to mine in Canada is extensive, with reserves expected to last for well over a century, according to Nutrien. The Allan facility is a source of pride in the local community and its single largest employer. Of the 680 people the facility employs, about 50 also farm.
“These are people who understand what the potash is used for and they want to produce a product that is going to apply effortlessly and do the job it’s designed to do,” says Rob Clayton, Nutrien senior vice president, retail North America. “I don’t think there are too many mines in the world where end users are also the people mining it.”
An Underground Community
The Allan mine is an integrated operation with office buildings, storage buildings, milling facilities, a tailings management area and tall head frames that house the surface and production shafts. The facility is operated by people with a diverse mix of training and skills, geologists, mine workers, engineers, administrators, and technicians.
The media’s journey into the Allan mine starts at the facility’s single service shaft, which connects workers and guests to the ore body below.
A large industrial elevator called a cage carries people, supplies and even vehicles and mining equipment (all of which has to be reassembled) to the underground operations. The cage travels down the shaft at roughly 437 yards per minute, moving the length of a football field in about 15 seconds.
The underground operation has roads, offices, electrical stations and repair shops. Vehicles transport workers from the service shaft to active mining areas, called a mine face, often miles away. The mine encompasses a large area, stretching 12.43 miles north to south and 9.32 miles east to west.
The natural temperature of the mine is a constant 81 degrees Fahrenheit, even in the middle of a Canadian winter.
“Everyone’s like, ‘how did we get a hot, salty sea in Saskatchewan?’ because it doesn’t make sense given our climate here,” says Zoe Belanger, Nutrien geologist.
The answer has to do with tectonic plates, large slabs of the Earth’s crust that slowly but continuously move.
Modeling indicates the seabed was once located roughly where the country of Peru is now, and through the shifting of tectonic plates, it wound up under Saskatchewan.
“It’s hard for a lot of people to wrap their minds around how it happened, but that’s plate tectonics, which is a whole interesting science itself,” Belanger says.
The earth continues to slowly shift deep in the Allan mine shaft, even as workers harvest the ore and send it above-ground. Dave Murray, shaft general foreman, cautions the media to not touch the sides of the shaft for safety’s sake.
The Valued Role Of Technology
Nutrien started extracting potash from the Allan mine in 1968. The work was laborious and dangerous, requiring the use of explosive charges. Today, the miners harvest the quartz-like ore – pinkish-red or white in color, depending on the vein – with 200-plus-ton boring machines, which cut into the mine face using a circular pattern.
All six of Nutrien’s mines have a number of borers operating at various locations simultaneously at any given time to produce a continuous supply of ore to feed the company’s processing mills.
It’s common for operators of the mining machines to need an hour to reach the rock face where they’ll work their shift, Belanger tells the media.
“That’s a big part of our logistics – trying to get more efficient in how we get those workers out to the face in a timely manner,” she says.
In 2019, Nutrien began adding tele-remote functions to its potash mining practices.
“The initial push to adopt the tele-remote function was for the safety of our operators. Improved efficiency was a byproduct,” says Frehlich.
The Allan mine currently has five borers set up to work via remote operators, who sit in above-ground offices and run the machines via computer. The process requires a level of sensitivity to work the borers via a toggle, one of the operators notes, as compared to hands-on use of the equipment.
Frehlich says the company plans to increase its use of the tele-remote function, as it has enhanced both safety and efficiency.
“It is increasing the utilization of our borers by allowing us to run through breaks and even through shift changes,” he adds.
From Extraction To Processing
As the potash is mined, a series of conveyors carries the raw ore to underground storage areas where it is kept dry until it can be hoisted to the surface for milling.
Large bucket containers called skips carry the ore to the surface. As one skip is being filled at the bottom of the shaft, a second skip is dumping ore at the top in a continuing cycle that takes about 90 seconds to complete.
Once the ore reaches the mill, Nutrien begins the process of transforming it into plant ready fertilizer. The milling process involves removing clays through scrubbing and cyclones.
“We crush it, then we slurry it, crush it some more, and then, through a flotation process, we remove the clays through cycling and scrubbing,” Frehlich summarizes. “Then, we separate the salt and the potash crystals through another flotation process. We just keep reprocessing to maximize our recovery of the potash,” he adds.
The potash is sized and separated through a system of oscillating screens, sifting through the different-sized crystals. Undersized crystals are pressed together, then crushed and screened again. This compaction process is repeated until the granules have a somewhat uniform size.
At this stage, the product can be sent to warehouses. From these facilities, plant ready potash can be shipped to buyers around the world.
“There’s a guaranteed analysis done with each one of those loads that goes out,” says Brian Knifong, head of marketing for North America for Nutrien. “We know for a fact that when the product comes out of the ground, is processed, then gets on a railroad car or shipping vessel to reach the retail facility, we have delivered a high-quality product that’s been extensively tested with strict criteria.”
Looking Ahead
Prior to the conflict underway in Ukraine, Canada was the world’s third-largest exporter of fertilizer in 2021, following Russia and China, according to Statistics Canada.
The war in Ukraine and sanctions on Russian potash have increased the demand for Canadian potash and highlighted its importance to global food security.
Rob Clayton says having continued regulatory harmony between Canada and other countries, especially the U.S., is important.
“The free flow of products, technology and information across the border is really important,” he says. “My message to our governments would be to continue helping all our farmers feed a growing planet.”
Clayton says that continues to be Nutrien’s focus now and for the future – delivering high-quality potash to help farmers grow the world’s food from the ground up.